Is getting a CNC router worth it?
- Phil Barrett
- Dec 1, 2019
- 3 min read
It's almost 2020 and hobbyist level CNC routers are plentiful and relatively inexpensive. Since the late 1970s, I've wanted one because of the promise of precision and accuracy. And the ability to create an object in CAD and cut it out exactly as designed. But up until the 21st century, they were simply too expensive. I even made an abortive attempt to build my own using iron pipe, angle iron and skate bearings. It sort of worked but had way too many issues and I gave up. Fast forward to about 2010 when all the parts started coming together - stepper motors, controllers, aluminum extrusions, linear guides and so on. The prices dropped and people started putting out consumer level CNC machines for less than $2000. Within a few years that had dropped to below $1000. It was at that point that I couldn't sit on the sidelines.
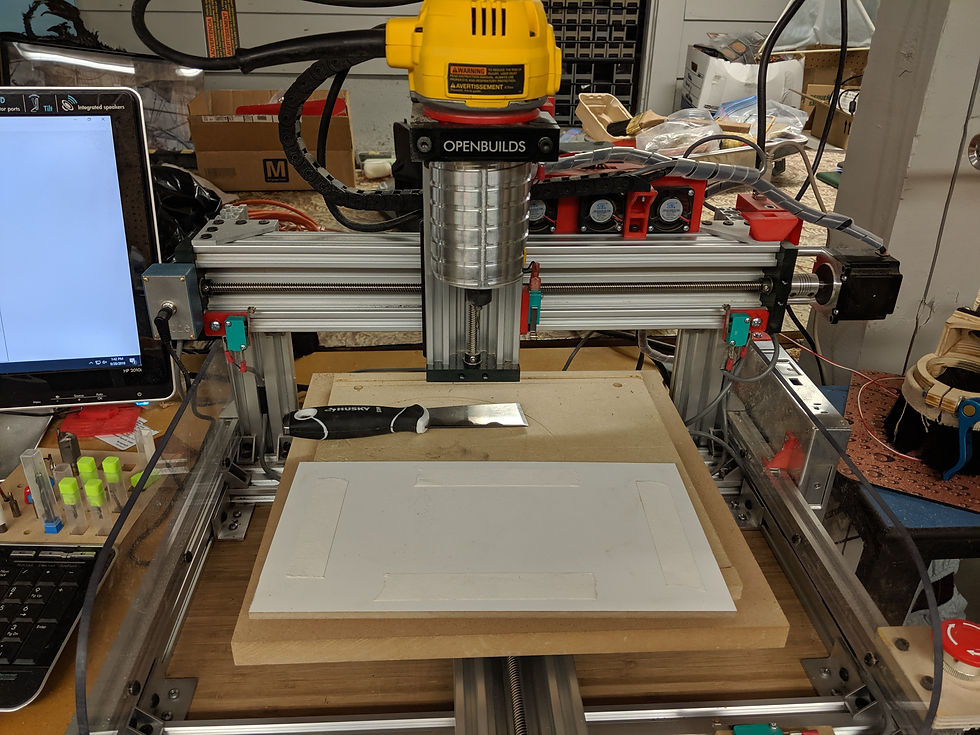
I still wasn't sure if a CNC machine would get the use that it needed to justify (in my mind, anyway) the cost. Read my earlier blog about "Should I buy that tool" for some background. So, I selected a small and inexpensive extruded aluminum router kit - CBeam Router. My main goal was to learn about CNC without making a big investment. It cost me around $600, uses an off the shelf router and has a work area of 320 mm X 280 mm (about 13" x 11"). Because of the low end materials used, it has a fair amount of flex. But with care in how you create your GCode (instructions to the router) you can over come the flex and make some pretty sophisticated things.
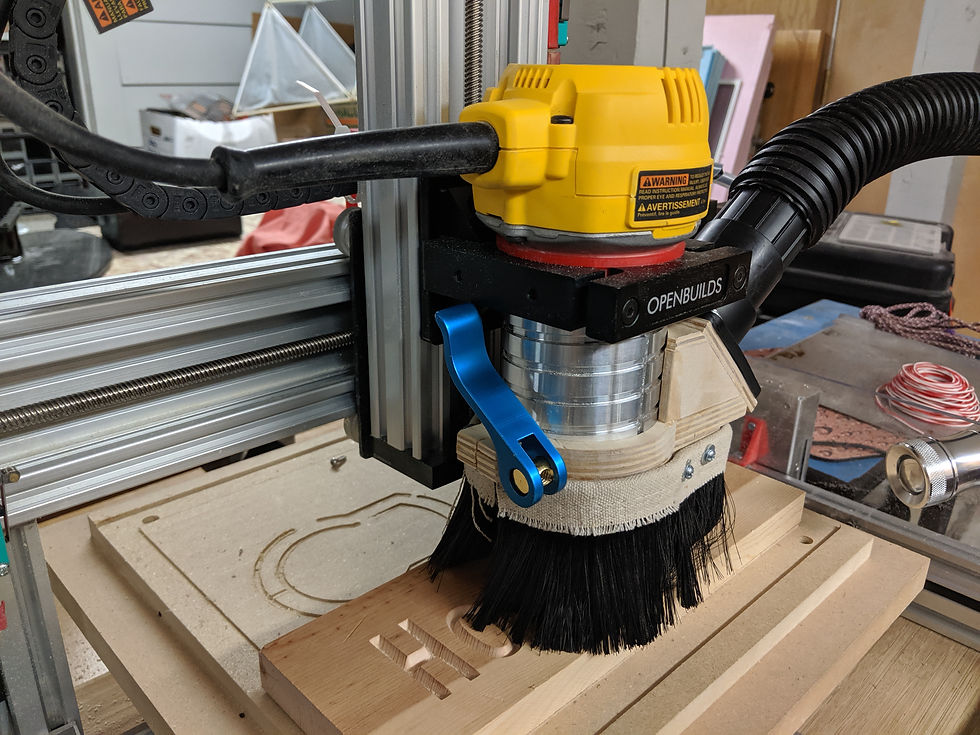
The first project was for a dust shoe. I'm a bit manic about dust collection in my shop and the CNC router was no exception. It took me two tries to get to something that I liked. In the process, I learned a lot about depth of cut, ramping, feeds and speeds. Probably the biggest lesson is that you can do a lot of things with even a cheap router but you have to slow it down. More expensive routers with greater rigidity can run much faster.
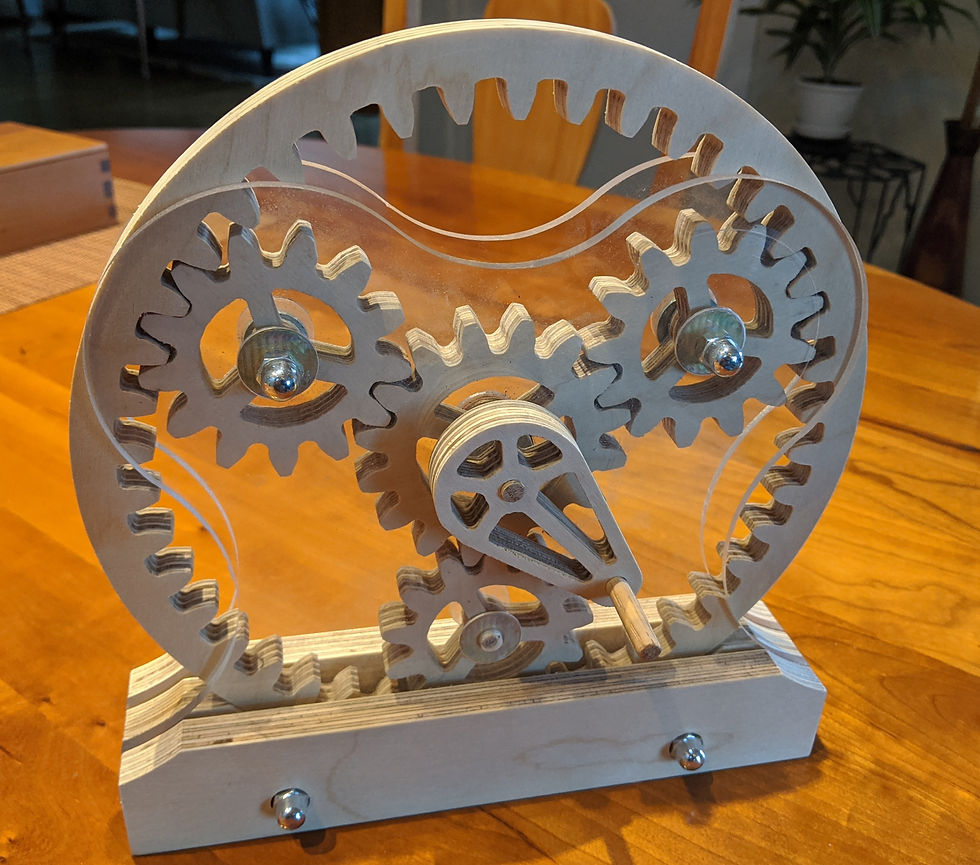
Then I made some signs. Small signs. They looked pretty good even with a simple font. Along the way, I turned out a number of router templates for non CNC projects I was working on. Then I discovered engraving and made some aluminum plant tags for my wife. At that point my "silly obsessions" became "neat project's Phil made" and the source of a little bit of pride on her part. I might have created a monster there. Then I made some gears that were a big hit. Every "Non CNC" project seems to get templates made on the machine. Pretty soon it was clear that the CBeam machine had become a core tool in my shop. It's helped me raise the level of precision on my projects. BC (before CNC), my templates were hand cut and while fairly good, had some imperfections. Now my templates are precise and perfect. New uses seem to come up daily.
So by now, the answer to the title question should be clear. However, my little CBeam machine is clearly insufficient for my needs. The work envelope is much too small and the amount of flex means slow going for even simple projects. Could I live with it? Sure. Do I want to? NO! So, I'm in the process of selecting a second CNC router. It will have a much larger work area and be more rigid to give me much faster cutting speeds. And, gulp, cost around 6 grand. I just have to make room in my shop which is easier said than done!
Comments